In ancient Rome, augurs spent hours watching the movements of birds to predict future events and advise magistrates based on their observations.
Luckily, Augury offers a more reliable approach.
WHAT DOES AUGURY DO?
A leader in machine health and process health solutions, Augury uses purpose-built AI technology to help manufacturing and industrial companies eliminate production downtime, improve process efficiency, maximize yield and reduce waste and emissions.
At Augury, seeing into the future is no longer the result of omens and magic but instead relies on cutting-edge technology including proprietary artificial intelligence. Product managers Dov Stern, Gila Corem and Naama Zarfati serve as modern-day oracles for Augury’s technology in service of the company’s mission: To empower industries with prescience.
“In tech, there’s a saying: product is the ‘why’ and sometimes the ‘what,’ and engineering is the ‘how,’” Stern said in explaining the product management roles that he, Corem and Zarfati hold. “As product managers, we’re responsible for the value.”
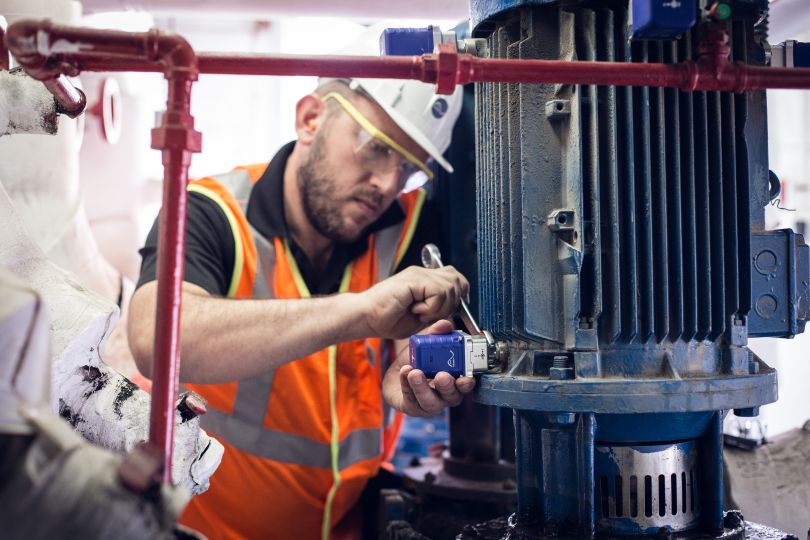
Stern spearheads the quest to detect faults and avert potential failures before they cast their shadows, with a particular focus on finding new opportunities for AI to deliver value to customers.
Recently, Stern’s team has unveiled a new feature they call “forcing frequency trends.” This feature, as Stern explained, deciphers the vibrations of machinery, akin to discerning notes from a chord.
“If you can figure out what frequencies are significant in the vibration signal then you can figure out what’s wrong with the machine — all the defects will happen at different syncopations,” he said. “This new feature calculates the speeds of all these components and allows you to pick out the amplitude of a specific frequency.”
“If you can figure out what frequencies are significant in the vibration signal then you can figure out what’s wrong with the machine — all the defects will happen at different syncopations.”
With the new feature, vibration analysts will be able to specify the frequencies they want to and compare them over time instead of having to manually pick out these frequencies. The tool will create a clean line graph of the frequency so analysts can see when the frequencies are deteriorating and understand what is wrong with the machine.
“It’s a hybrid intelligence approach to machine health,” Stern explains. “We’re letting the user point to what’s relevant in their machine, personalize their diagnostics and improve accuracy a great deal.”

Gila, part of Augury’s Alliances team, is largely focused on the company’s collaboration with Baker Hughes, a titan in the energy domain. Augury provides Baker Hughes with a purpose-built, AI-powered algorithm that generates equipment diagnostics from sensing system data.
“We created a whole new architecture that sends that data from the sensing system to Augury’s platform and AI diagnostics and then displays the insights in the platform,” Corem explained.
The journey to launch was not without hurdles, though.
“One of our biggest successes occurred after our biggest failure,” Corem said. “The first iteration of this product was with a different architecture that we realized was a dead end — it wasn’t going to provide good value for customers.”
She continued, “We had to explain that to both companies — not an easy conversation — and start from scratch with a different approach. We saw right away that it was working. Just after our first installation with a customer, the sensor discovered an issue with a machine very quickly, so we knew we had our proof.”
Finding a smooth course through difficult conversations and challenges large and small is just part of the job for Corem as she works to build trust between the two teams.
“Our two companies are very different: we are a smaller U.S.-Israeli tech company and they are a large American corporation. There are big cultural differences there that need to be understood and bridged,” she said.
In order to bridge those differences, Corem and her team established a forum for project managers, customer success managers, field engineers and solutions architects from both companies, allowing them to discuss problems and propose solutions. With a central hub for information and knowledge sharing, the forum became a productive engine for driving the project forward.
Collaboration wasn’t only virtual, though. The two teams came together for a meeting in Florence, Italy, after a customer installation.
“We were so lucky because it gave us an opportunity to celebrate the win together with team members from around the world,” Corem recalled. “It was a big boost in establishing relationships, building trust and moving forward with other decisions we needed to make.”
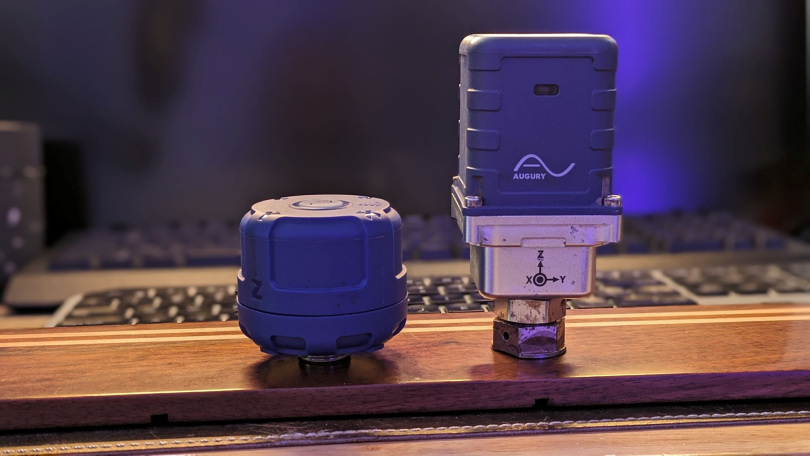
On the machine health hardware IoT team, Zarfati is exploring what she calls a “next-generation gateway” in partnership with a leading IoT company.
The machine health hardware IoT team’s main focus is improving how data is collected and transmitted from sensors to Augury’s algorithm in the cloud, where the AI analysis happens.
Zarfati herself focuses on connectivity and its associated challenges — network coverage, sensor battery lifetimes, electrical infrastructures, security and more.
“The connectivity process might sound straightforward, especially when you think about our phones, but in an industrial area the challenges are quadrupled,” she said. “There are often tradeoffs that need to be made while ensuring we give customers quick and reliable insights into their machines.”
Augury’s new gateway is a powerful and reliable product that also requires less electrical infrastructure than the current solution, Zarfati explained.
“It is a best-in-class solution that will enable very stable connectivity, and we are defining its requirements based on customer needs coming from extensive field experience,” she said.
As launch day beckons for Zarfati and her team, their journey underscores the spirit of innovation and collaborative ingenuity that drives them.
“Relationships are key for collaboration, especially when you are solving a problem,” she noted. “We had an issue come up with our current solution that required the work of other product managers as well as constant collaboration with the go-to-market team, field and services teams and customer calls on top of our regular work. Having close relationships kept us on track.”
Across teams, this commitment to relationship building remains constant, and Stern expressed how understanding diverse perspectives helps foster collaboration across perceived boundaries.
"Communication becomes vital, and we made that a priority every day," he said.